Spray drying 2
Application : Food industry.
Issue : Internal parts worn after 4 - 8 hours, unstable drying process due to pressure loss on nozzles.
Solution : Selecting and applying proper material for internal parts after research wear mechanism.
Result : Stable drying process and parts are now lasting for 3+ months.
Details :
A recently commissioned spray dryer in the food industry suffers from aggressive media. During start up and process liquids are being used that cause heavy wear on the internal parts of the spray drying nozzles. Usually the pump pressure drops after some 4 - 8 hours of production. This is an undesired effect on production, becoming even worse due to the increase in droplet size during process, causing unstable batches in terms of powder particle size. Customer approached SWM for internal parts made of industrial diamond.
We are able to manufacture internals in industrial diamond, but always assess the wear mechanism first. Until now, it has never been necessary to use parts made of diamond.
Analysis of the used parts showed that both material, as well as the finishing of the parts were poor. The wear mechanism proved to be chemical corrosion and as a result of that extreme abrasion.
By applying our standard material, which can resist a wide range of Ph-values, and the proper mechanical finishing for highly corrosive liquids the life span of our wear resistant parts adds up to 3-4 months.
Within a brief period after exchanging the internals customer finally could enjoy a stable production process without applying very expensive diamond parts.
An extra advantage:
Consumption of cheap wear parts before exchange amounted to a little less than € 100.000 per annum. We reduced this by applying our wear resistant parts to less than 10% of that amount.
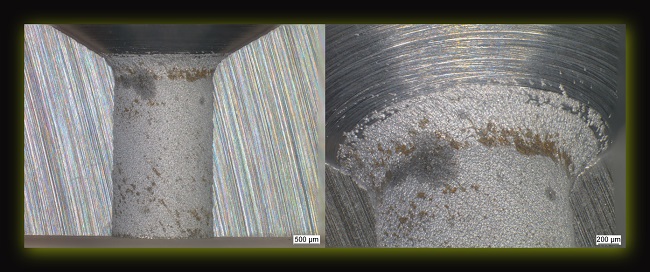
Clearly visible, high wear due to wrong material selection.